Finding the solution to a problem
Our team of problem solvers, also known as the Like Tech team, have been reunited as our work for the Heysham 2 outage is complete. For some of them, it was their first outage describing the experience as “interesting”, “a learning experience” and “eye opening”. It’s one thing to be told what to expect from an outage but it’s another thing to experience it first hand. With any outage, you have to expect the unexpected. Not everything will go exactly to plan and there may be some delays. Our team know this and possess the ability to adapt and come up with the solutions.
Now the team are back, they have picked up projects that are paused when there is an outage, others are working through the repairs and one experienced member of the team has completed a comprehensive training plan for our newer team members. The 8 days of training is delivered over 4 weeks and has been planned by our senior engineers to upskill our team and ensure knowledge gets passed on and doesn’t become obsolete. The training is also suitable for other local electech companies.
Speaking about the training, Zac from Current Conductors said;
“It was definitely the best course I have been on so far, I learnt a lot of great things that I am now putting into practice, I have already seen a huge change in the way I am working, my fault finding is much more methodical and logical. Nigel is one hell of a teacher, I not only learnt from him in the lessons but we had some really good chats during the breaks about circuit problems I have faced/am facing. He’s a great guy to be around.”
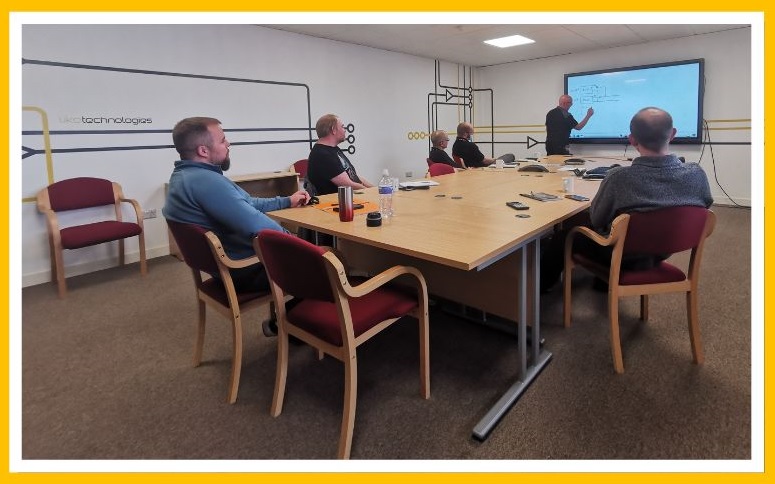
This summer we’ve also invested in software, hardware and training from ABI Electronics Ltd to enhance our problem solving capabilities. This investment means many of the fault finding tasks that would previously take days, should now take hours. It also means we’ll be able to take on some repairs that we have previously had to turn away.
ABI Electronics Ltd is the world’s leading supplier of specialist electronic test and measurement equipment, and a renowned contract electronics manufacturer. All ABI products are designed and manufactured at its premises in Yorkshire, UK and have been exported all over the globe for over 35 years.
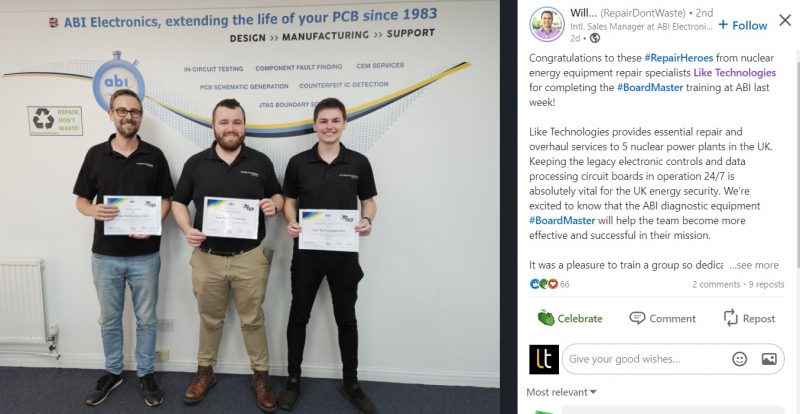
Creators of the Repair, don’t Waste! movement, which started as a hashtag in 2015, their flagship website was launched in February 2022. The movement aim is to highlight the importance of implementing a repair-first approach in every industrial business and educate those in the industry who may not be engineers themselves but are looking for a solution to their faulty PCB troubles. Multiple international organisations around the world like Collins Aerospace or Schindler have embraced the movement and have contributed to the reduction of E-Waste that is generated every year.
Have a problem that needs solving? Send us an email with a brief description of the problem and a photo (if relevant) and someone from the Like Tech team will get back to you. Prefer to pick up the phone? Call us on 01524 811383