Simulation Success
At Like Technologies, we’re a dedicated team of hardware and software engineers with long standing partnerships in the nuclear industry. Our teams quite often collaborate on projects together to ensure synergy between hardware and software solutions, one area they work on is simulations.
Simulations are used across many different industries and sectors, often for training purposes but in industries such as nuclear, they can be vital for testing purposes as well. Our team of engineers, led by our software engineers, regularly work on a simulation of a nuclear power station.
Siemens recently discussed why simulation driven design is essential for electronic engineering, describing it as cheaper, faster and better.
Why our client needed a simulation
At any one time there can be around 12,000 electronic signals sent in a nuclear power station that need to be converted into engineering units, and displayed in a way that the human eye can process and understand. This takes place in a control room, using a significant number of micro and supermini computers. Our clients development/test system has a full complement of superminis, but only has a limited selection of micros.
“In order for us to be able to test modifications that we make to the production system, we need to frequently change micro configurations. This is an intensive task, and it can take several days to fully reconfigure a micro. If we had a full complement of micros available, we could probably complete all testing in a few days, however with the additional overhead of having to swap micro configurations on the test system, it can take 4 or 5 weeks to complete testing.”
Bryan Hobson, Lead Software Engineer/ Senior Engineer
Once the simulation was built, our team were able to reverse engineer the signal flow between the micros and the superminicomputer (aka supermini) to enable a more realistic test environment. As standard, regular testing wouldn’t allow us to change the variables as if it was tested live it could present catastrophic consequences. This simulation enabled the engineers to control the 12,000 electronic signals and safely test some ‘worst case scenarios’.
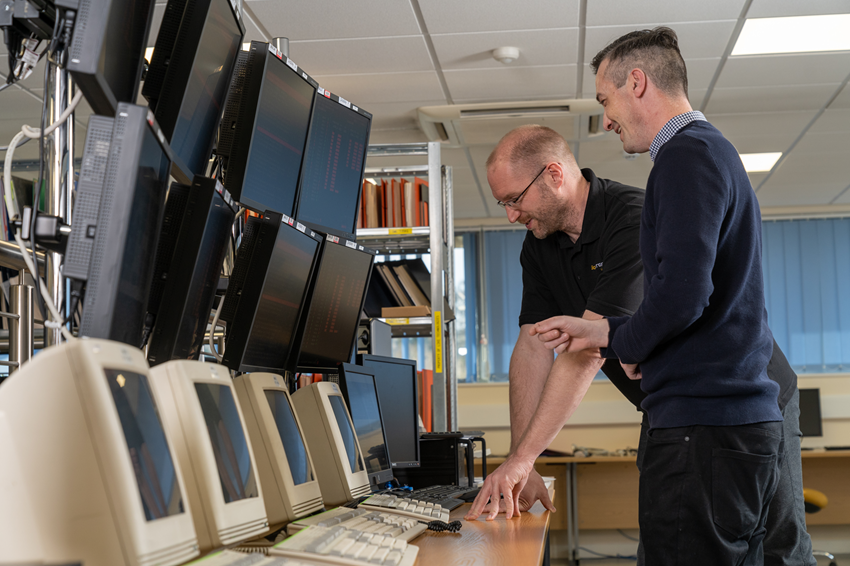
Making Progress
“We were now able to interact with the simulator, for example we could trip the reactor or drive control rods and see the effect on the DPS screens. It became easier and faster for us to test software changes on the superminis, however it didn’t allow us to test micro software changes. As our micros were emulated, they couldn’t run the normal micro software that we maintain on the production system, nor could we test configuration changes“.
Bryan Hobson, Lead Software Engineer
As the project progressed, whilst the team were able to emulate a micro to test configuration changes, they were not able to test how these changes would affect micros that were being used in the control room on a daily basis. The need to have real micros became the driver for this project.
The Solution
Having a team with hardware and software skills our software team were able to speak to the hardware team to look for a solution to the problem of the micro shortage.
“In a nuclear power station there is one control room per reactor. Each control room could house up to forty micros, all reading different inputs and having various controls. One micro can contain up to five PIBUS crates with each crate containing sixteen cards each with sixteen inputs. You can see how things starts to multiply, adding complexity and time to any testing of a minor or major configuration change. Our solution was a hardware interface card, developed in house, that replaces a full crate of PIBUS cards.”
Melvin Park, Lead Hardware Engineer/Senior Engineer
Using a hardware interface card alongside the software we had previously developed enables us to configure a real micro to be any other micro within minutes. This means that we could easily test modifications to all parts of the DPCS and easily switch micro configurations around within minutes.
This project is ongoing and demonstrates how new technology can work with older technology, and the need for hardware and software solutions – it’s often not one or the other. Collaboration is increasing in our industry and is something we support internally and externally.
By working with Like Technologies the benefit for our client alongside our industry knowledge was our in house hardware and software skills. Being quite literally next door to one another, the two teams were able to work together to come up with a solution in a time efficient manner and be a single line of communication for our client.
If you work in an highly secure or regulated environment that requires regular testing, could a simulation bring you more testing success? Call us on 01524 811 383.